You can find them on all the highways and in every parking lot around the world – we’re talking about axles. Vehicles can’t operate without them… so it should be no surprise that MTI helps join millions of axles each year with friction welding.
For decades, axles have been joined with Direct Drive Friction Welding, but could there be ways to improve the process by using our newest joining technology, Low Force Friction Welding?
In this episode of Whiteboard Wednesday, we’ll take a closer look at our legacy technology and stack it up against our newest technology to help you decide whether Low Force Friction Welding could ultimately help save you time and money.
A PROCESS FOR ALL AXLES
“Axle” is a broad term – and in the world of friction welding, we are either welding a spindle to a tube or housing (sometimes referred to as a banjo housing) or we are welding a flange to a tube.
One of the reasons axles are joined with Direct Drive Friction Welding is because they’re made from a hardenable steel. Our goal with Direct Drive Friction Welding is to apply a lot of heat into the axle so we can:
- Control the cooling rate
- Avoid the formation of martensite
- Improve fatigue performance
DIRECT DRIVE: HOW IT WORKS
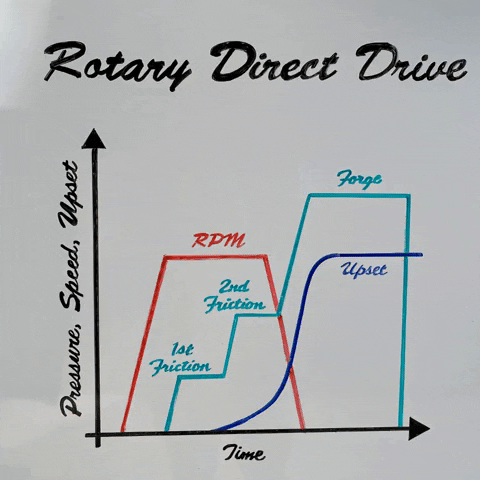
The Direct Drive Friction Welding Process consists of a few steps – let’s break them down.
In the first friction phase, we bring the spindle or flange up to a rotating speed (the set RPM), then the two parts come into contact under low pressure. This may clean up dirty parts, square the interface, and reduce the amount of friction so we don’t stall the motor when we bring on a higher load.
In the second friction phase, we have a higher load and are building more heat – this is where we start upsetting the component. In Direct Drive Friction Welding, this second friction phase is going to be much longer because we want more upset in order to drive more heat into the component, allowing us to control the cooling rate.
Once we achieve the desired amount of upset, we bring the spindle down to zero speed then we bring on forge force, completing the weld.
Let’s take a closer look at a specific application joined with our legacy technology.
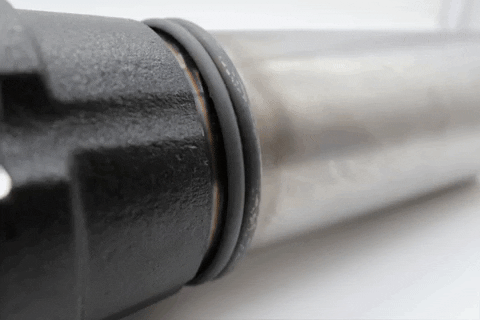
Axle tube to flange friction welded with Direct Drive.
This application is a tube to a flange (utilized in both combustion engine and electric vehicles). You can see the flash curl – but that curl will increase in size as the part increases in size. Because the flash curl is tight, it’s difficult to remove – sometimes it’s sheared off or sometimes it’s turned off with a two-axis flash removal process.
Now that you understand how we bring it all together with Direct Drive Friction Welding, let’s take a look at how the process changes during Low Force Friction Welding.
JOINING AXLES WITH LOW FORCE FRICTION WELDING
When utilizing Low Force Friction Welding, we don’t need to build the heat under load, we can do it with a pre-heat operation.
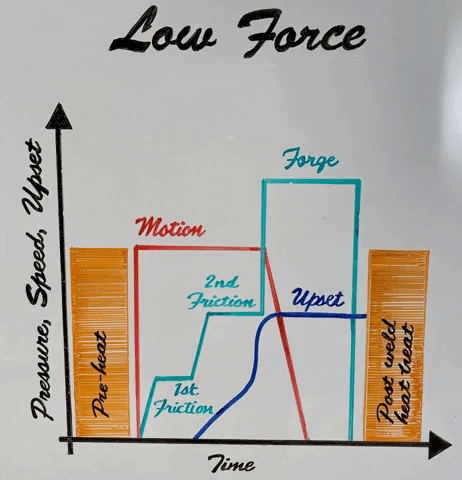
In this process, we can bring on a first friction or second friction phase or we can bring on full forge load from the beginning. Either way, our heat is driven from an external source, which enables us to add in the heat very quickly, thus reducing our cycle time.
Because of the pre-heat process, we are also able to reduce the amount of upset to achieve the same weld – an extremely valuable benefit for axle production.
If necessary, we can also choose to add a post-weld heating operation if we need assistance in controlling the cooling rate based on how we added the heat at the beginning.
Let’s take a look now at a sample weld created by Low Force.
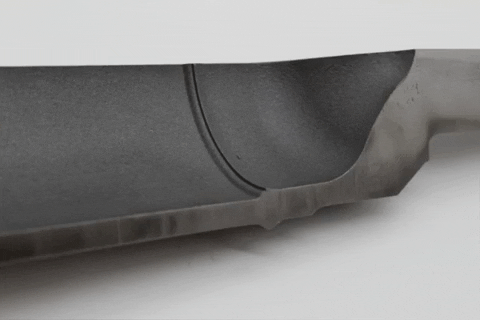
Large diameter E-Axle tube Low Force friction welded to a spindle.
This is a large diameter tube being welded to a spindle – a traditional axle application. With Low Force Friction Welding, there’s very little upset. You will notice there is a small bulge instead of a large flash curl.
We cannot remove the ID (inner diameter) flash, but you will notice the same bulge on the inside. As a result, the weld hasn’t generated a big stress riser, allowing us to achieve improved fatigue performance.
Axles are designed based on their fatigue performance, so if we don’t need to strengthen the weld because of the stress riser, we can decrease the wall thickness of components, thus providing a lightweighting opportunity.
IMPROVING THE PROCESS AS A WHOLE
As you look at an axle application, it’s important to consider the entire manufacturing process – and even part design – if you want to take full advantage of the value of Low Force Friction Welding.
For example, because we can achieve welds with lower upset, we can take a closer look at your manufacturing process to determine whether you can remove equipment out of your manufacturing line instead of just replacing your Direct Drive machine with a Low Force machine.
WE’RE WITH YOU EVERY STEP OF THE WAY
Wondering whether Low Force may be right for you? At our global headquarters in South Bend, Indiana, we can perform the Low Force welds on our machines and walk you through the weld development process. We can also provide you with parts that you can test on your own.
The ultimate goal is to help you redesign your manufacturing process to drive cycle times down and the value of the components up.
What are you waiting for? Let’s talk about your axles. Reach out to one of our knowledgeable sales engineers today to begin your Low Force Friction Welding journey!
Website: https://www.frictionwelding.in/
LinkedIn: https://www.linkedin.com/company/manufacturing-technology-inc/
YouTube: https://www.youtube.com/c/ManufacturingTechnologyIncMTIJoiningSolutions/videos