Welding Innovation for the Road Ahead
Friction Welding for Automotive Components
- 60-Ton Direct Drive Machine for Heavy Duty Driveshafts
Why Friction Welding is Vital for Automotive Applications
Friction welding is widely used in the automotive industry due to its seamless integration into automated production lines, meeting the industry’s high-volume requirements efficiently. With benefits like a full-depth bond and a minimized heat-affected zone, friction welding has become a preferred method for joining components in automotive applications.
FWT machines support a diverse range of automotive applications, including piston rods, turbochargers, cylinder rods, gears, drive shafts, and axles.
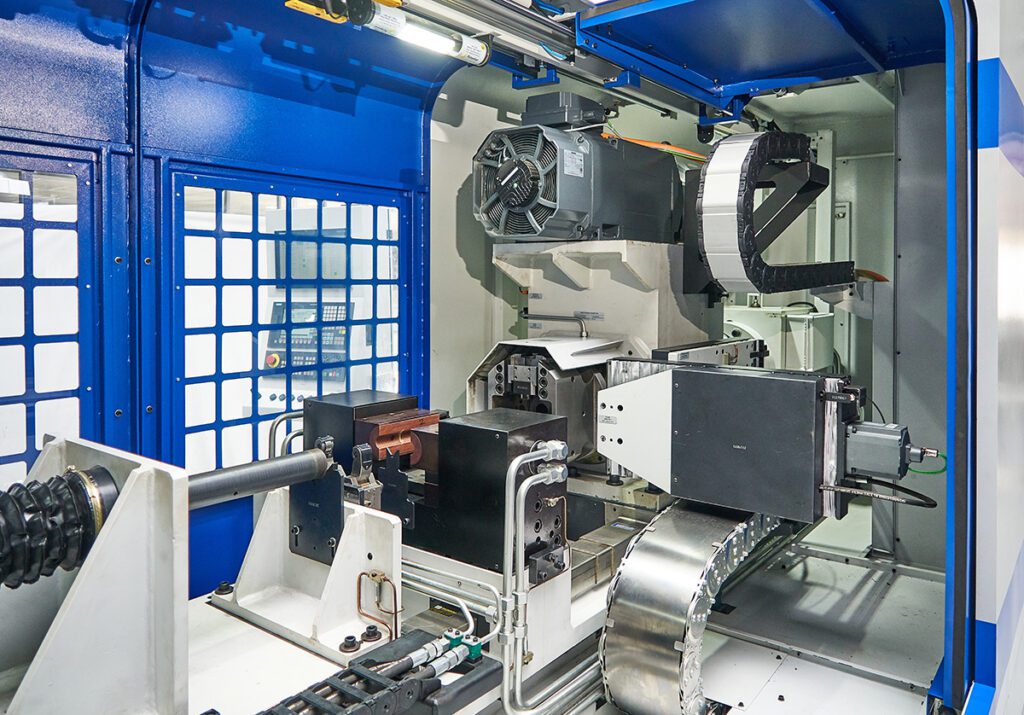
This photo shows an FWT-60 machine built to weld Piston Rods.
Advantages & Benefits
Driving Innovation in Automotive Manufacturing
FWT’s advanced friction welding solutions are transforming the automotive industry. Our technologies offer a range of benefits that enhance vehicle performance, reduce costs, and support sustainable manufacturing practices.
Bimetallic Joining
Bimetallic friction welding benefits the automotive industry by enabling the joining of dissimilar metals, optimizing the use of lightweight and high-strength materials to enhance vehicle performance and fuel efficiency. This process provides strong, reliable joints without the need for additional fillers or adhesives, reducing manufacturing costs. It also improves corrosion resistance and extends component lifespan.
Lightweighting
Lightweighting with friction welding benefits the automotive industry by reducing vehicle weight through the use of bimetallics, which improves fuel efficiency and reduces emissions. The process creates strong, durable joints without adding excess material, supporting the use of lighter materials like aluminum. This enhances vehicle performance and handling.
Automated, Efficient Process
Friction welding is an automated process that removes the occurrence of operator error resulting in higher process efficiency. Friction welding uses predetermined calculations and measurements, all mechanically operated, that keep quality as consistent as the first weld. Additionally, friction welding cells can accommodate a fully automated work cell with the use of robots and gantry systems.
Green Technology
Friction welding is an eco-friendly technology that does not emit smoke, fumes, or gases. Friction welding does not require consumables such as flux or filler material, reducing your carbon footprint all the way down your supply chain as less material and energy is used.
Bimetallic friction welding benefits the automotive industry by enabling the joining of dissimilar metals, optimizing the use of lightweight and high-strength materials to enhance vehicle performance and fuel efficiency. This process provides strong, reliable joints without the need for additional fillers or adhesives, reducing manufacturing costs. It also improves corrosion resistance and extends component lifespan.
Lightweighting with friction welding benefits the automotive industry by reducing vehicle weight through the use of bimetallics, which improves fuel efficiency and reduces emissions. The process creates strong, durable joints without adding excess material, supporting the use of lighter materials like aluminum. This enhances vehicle performance and handling.
Friction welding is an automated process that removes the occurrence of operator error resulting in higher process efficiency. Friction welding uses predetermined calculations and measurements, all mechanically operated, that keep quality as consistent as the first weld. Additionally, friction welding cells can accommodate a fully automated work cell with the use of robots and gantry systems.
"Near-net shape” components can be created through Linear or Rotary Friction Welding, requiring minimal additional machining, saving costly time and materials. Airframe structures and blisks used in jet engine assemblies are two examples of parts created through near-net shape joining.
Our Commitment
Quality is at the core of our innovation
With an in-house innovation team and a substantial investment in R&D, we continuously set new industry standards in quality, systems, and best practices. Our commitment to excellence is reinforced by our ISO 9001:2015 certification. For customers in Europe, FWT machines are designed and manufactured to fully comply with European safety requirements for CE.
Friction Welding Machines for the Automotive Industry
Friction welding machines are proven to produce high-volume, consistent-quality welds for turbochargers, cylinder rods, and more. No matter the size of your project, our friction welding experts will collaborate with you to provide specs to begin or help you build a customized friction welder solution.
Friction Welding Machines for the Automotive Industry
Friction welding machines are proven to produce high-volume, consistent-quality welds for turbochargers, cylinder rods, and more. No matter the size of your project, our friction welding experts will collaborate with you to provide specs to begin or help you build a customized friction welder solution.
ROTARY FRICTION WELDING
Our legacy in rotary friction welding, Direct Drive, is the automated solution for parts such as piston rods, axles, and more.
FRICTION STIR WELDING
Friction Stir Welding is vital for sensitive automotive parts to ensure driving safety. We use this type of welding to seal high-strength battery trays and heat exchangers.

Explore Our Parts Gallery
View our parts gallery to find the perfect applications, materials, and geometric fittings for your next project.
Contract Manufacturing Services
If you have a project in mind, we’re here to optimize your friction welds. From contract manufacturing to metallurgical, weld development, pre and post-weld services, we can help you achieve your production goals whether you need a few parts or many.
Contract Manufacturing Services
If you have a project in mind, we’re here to optimize your friction welds. From contract manufacturing to metallurgical, weld development, pre and post-weld services, we can help you achieve your production goals whether you need a few parts or many.
Learning Center
Case Study
Videos
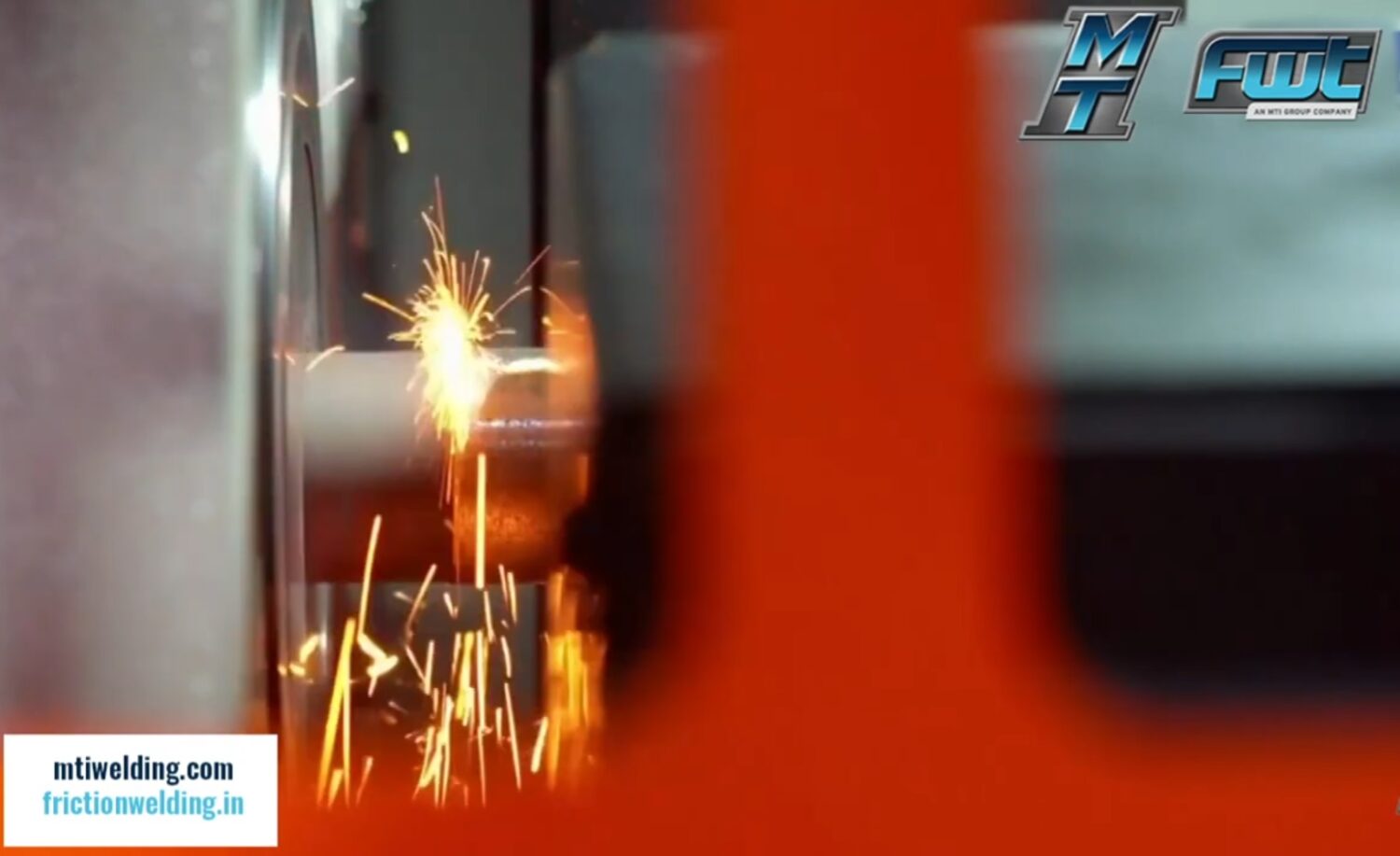
Direct Drive
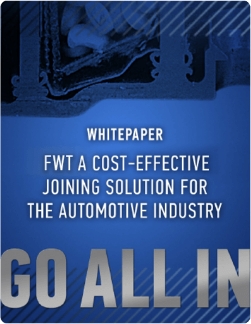
FWT White Paper
FWT: A cost-effective joining solution for the automotive industry
In the following pages, we will outline the benefits of friction welding, define the different types of friction welding, and describe the friction welding process. We’ll also mention current issues faced by the automotive industry. And finally, we’ll show how FWT is an effective tool to overcome these challenges and achieve manufacturing goals.