Innovative Welding for Sustainable Mobility
Friction Welding for Electric Vehicle Components
Why Friction Welding is Vital for EV applications
Friction welding is vital for EV applications because it allows for the reliable bonding of lightweight and dissimilar materials, which are crucial for enhancing vehicle range and performance. Friction welding creates high-strength joints without melting materials, reducing the risk of defects and ensuring the structural integrity of components like battery housings, electrical connections, and drive shafts.
FWT plays a pivotal role by providing advanced friction welding solutions that address the unique challenges of EV manufacturing.
Friction Stir Welding demonstration of an automotive electronics enclosure.
Advantages & Benefits
Powering the Future of Electric Vehicles
FWT’s advanced friction welding technologies offer numerous advantages that can revolutionize EV manufacturing, from enhancing vehicle range to improving sustainability.
Lightweighting
One of the biggest selling points for an Electric Vehicle is its operating range. In other words, the number of miles it can travel before needing a recharge. A heavier car can’t travel quite as far, so that’s why many EV manufacturers place such a strong emphasis on lightweighting. Friction welding can deliver lighter parts by incorporating the use of bimetallics or opting for lighter materials such as aluminum.
Bimetallic Joining
Friction welding gives us the ability to join dissimilar metals, a substantial advantage for lightweighting. Instead of using only one type of metal for a part, manufacturers could switch to a lighter material for a less critical portion of the part and use a heavier material for the heavy-duty portion only. This not only provides substantial performance benefits, but cost savings along the way.
Eco-friendly
The rise of electrification is largely due to the desire to become more sustainable and responsible in our manufacturing practices. Friction welding itself is a green technology that emits no smoke, fumes, or gases and uses no flux or filler material. Additionally, friction welding uses less energy than other joining methods, all of which contribute to a reduction in your carbon footprint and help achieve your going green goals.
Watertight Seals
Friction stir welding delivers parts with watertight seals, ensuring the integrity of battery enclosures and electronic components by protecting them from moisture and environmental contaminants. The solid-state welding process produces high-quality, leak-proof joints without the need for additional sealing materials, reducing assembly complexity and costs. This reliability enhances the safety and longevity of EV components, crucial for maintaining vehicle performance and reducing maintenance requirements.
One of the biggest selling points for an Electric Vehicle is its operating range. In other words, the number of miles it can travel before needing a recharge. A heavier car can't travel quite as far, so that's why many EV manufacturers place such a strong emphasis on lightweighting. Friction welding can deliver lighter parts by incorporating the use of bimetallics or opting for lighter materials such as aluminum.
Friction welding gives us the ability to join dissimilar metals, a substantial advantage for lightweighting. Instead of using only one type of metal for a part, manufacturers could switch to a lighter material for a less critical portion of the part and use a heavier material for the heavy-duty portion only. This not only provides substantial performance benefits, but cost savings along the way.
The rise of electrification is largely due to the desire to become more sustainable and responsible in our manufacturing practices. Friction welding itself is a green technology that emits no smoke, fumes, or gases and uses no flux or filler material. Additionally, friction welding uses less energy than other joining methods, all of which contribute to a reduction in your carbon footprint and help achieve your going green goals.
Friction stir welding delivers parts with watertight seals, ensuring the integrity of battery enclosures and electronic components by protecting them from moisture and environmental contaminants. The solid-state welding process produces high-quality, leak-proof joints without the need for additional sealing materials, reducing assembly complexity and costs. This reliability enhances the safety and longevity of EV components, crucial for maintaining vehicle performance and reducing maintenance requirements.
Our Commitment
Quality is at the core of our innovation
With an in-house innovation team and a substantial investment in R&D, we continuously set new industry standards in quality, systems, and best practices. Our commitment to excellence is reinforced by our ISO 9001:2015 certification. For customers in Europe, FWT machines are designed and manufactured to fully comply with European safety requirements for CE.
Friction Welding Machines for the Electric Vehicle Industry
Electric Vehicles face different challenges than traditional vehicles. But with the right welding machines, engineers and manufacturers can advance to more efficient and environment-friendly vehicles. FWT friction welding ensures the vehicle’s structural integrity, battery performance, and optimal mileage before the next recharge. Our machines come in semi- and fully automated solutions.
Friction Welding Machines for the Electric Vehicle Industry
Electric Vehicles face different challenges than traditional vehicles. But with the right welding machines, engineers and manufacturers can advance to more efficient and environment-friendly vehicles. FWT friction welding ensures the vehicle’s structural integrity, battery performance, and optimal mileage before the next recharge. Our machines come in semi- and fully automated solutions.
ROTARY FRICTION WELDING
We specialize in all forms of Rotary Friction Machines, from Direct Drive and Inertia to Hybrid.
FRICTION STIR WELDING
FWT’s world-class friction stir welding technology ensures water-tight seals and material cost-savings.
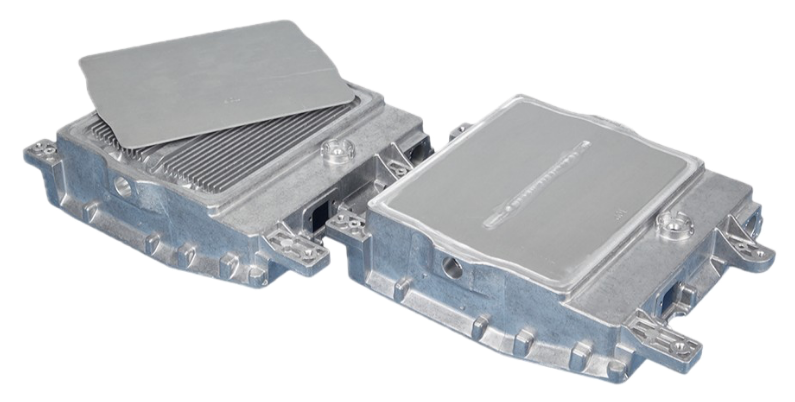
Explore Our Parts Gallery
Wondering if your Electric Vehicle components can meet the required shapes and materials? Our parts gallery holds the key to your innovation. Explore our gallery to find the perfect applications, materials, and geometric fittings for your next Electric Vehicle project.
Contract Manufacturing Services
Whether you need to have a part designed and manufactured or you need to have a friction welding machine built, FWT has state-of-the-art machines and expertise to make it happen. Our global Contract Friction Welding teams handle your project from start to finish, from consultation, design, construction, maintenance, and training.
Contract Manufacturing Services
Whether you need to have a part designed and manufactured or you need to have a friction welding machine built, FWT has state-of-the-art machines and expertise to make it happen. Our global Contract Friction Welding teams handle your project from start to finish, from consultation, design, construction, maintenance, and training.
Electric Vehicles Friction Welding Machines for R&D
Ramp Up your Innovations with our R&D Machines
FWT has in-house friction welding machines to meet your research and development needs. Explore and innovate with various materials and applications for lighter vehicle weight and better engine and battery performance.
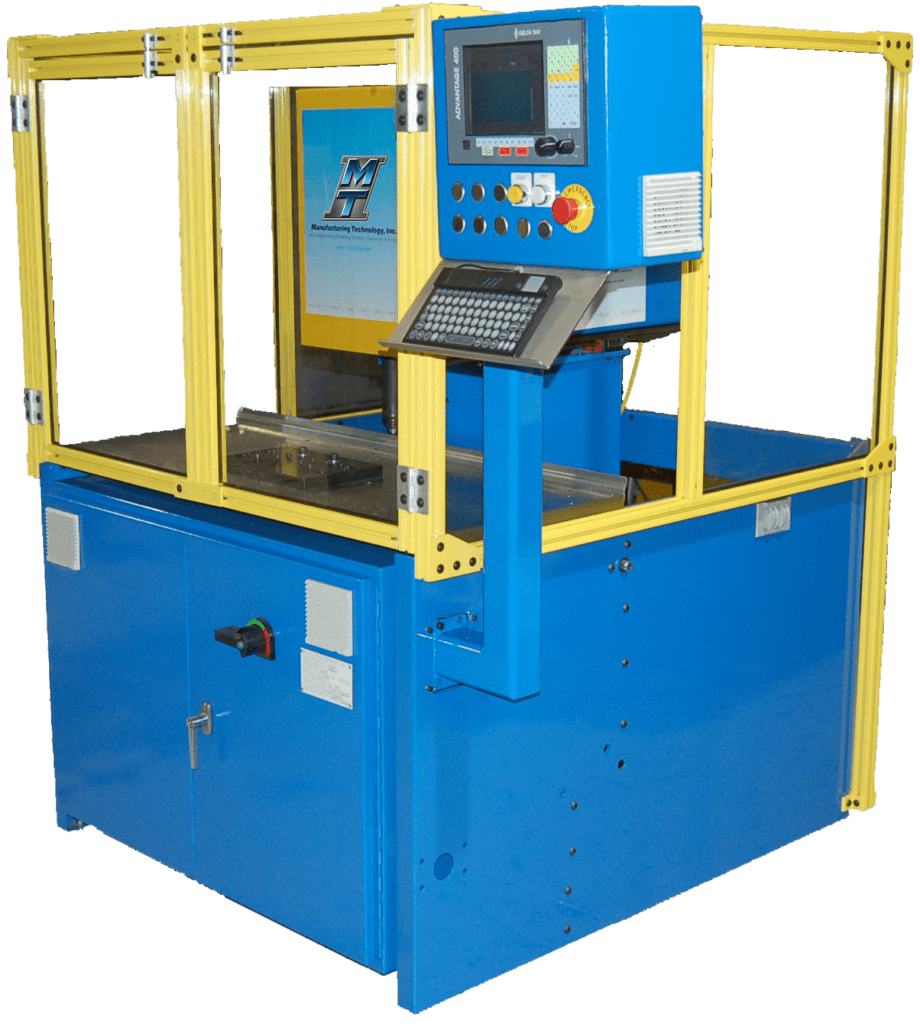
FWT’s PM-0 Friction Stir Welding machine, available for in-house R&D and production.
Learning Center
Case Study
Videos
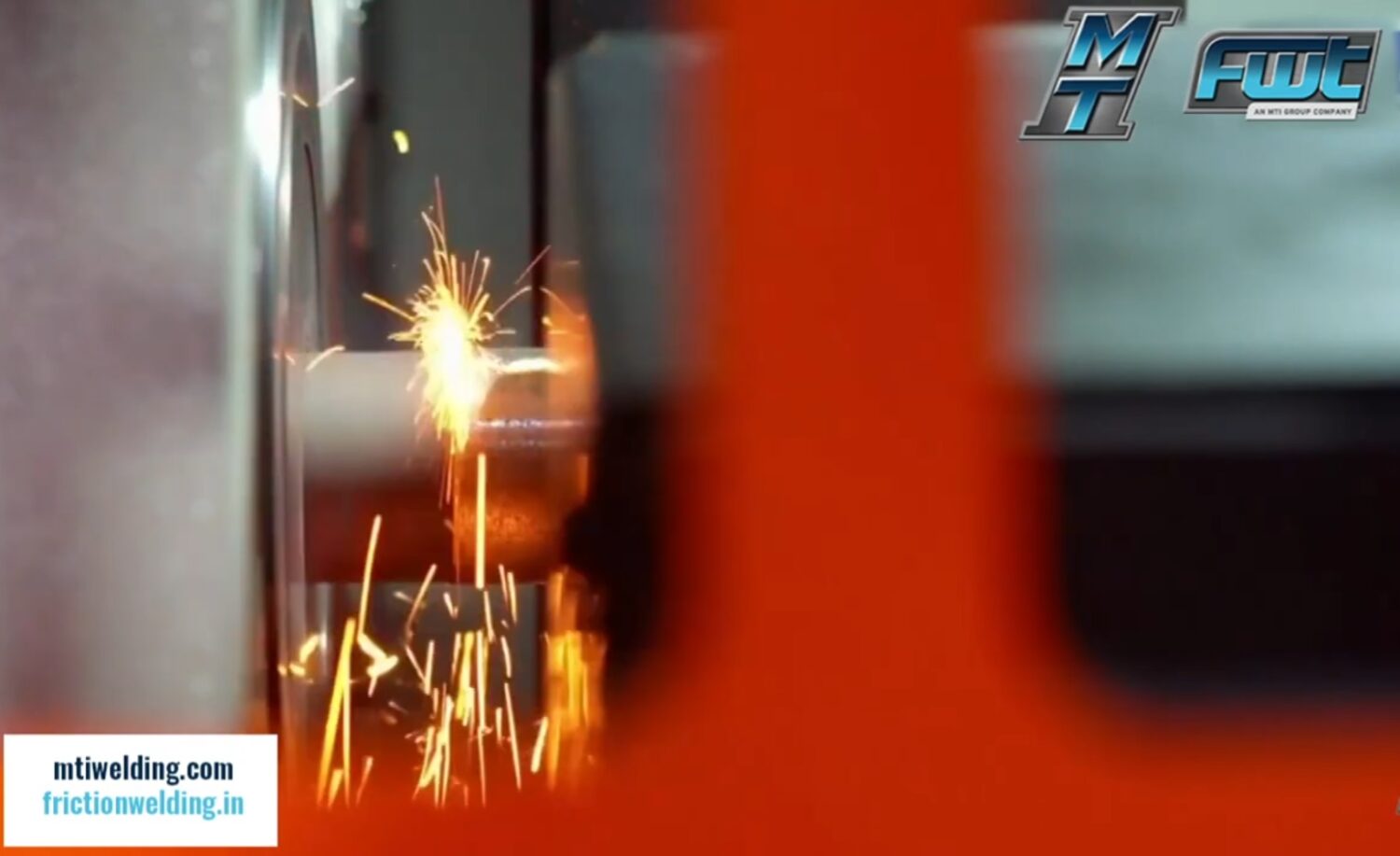
Direct Drive