Welding Strength for the Energy Sector
Friction Welding for Oil & Gas Applications
Why Friction Welding is Vital for Oil & Gas Applications
Since a typical string of drill pipe can be three to four miles long, composed of 30-foot sections, weld integrity is a must in the oil field drilling industry. Friction welding supports the lower drill stem assembly (made up of other drill pipes, drill collars, and the drilling bit) and transmits the rotary torque needed for drilling. Friction welding produces a metallurgical bond strong enough to take the high torque and highly loaded rotary tension due to directional drilling.
Whether you want to improve a component, have one designed or manufactured for you, or have a friction welding machine made for your needs, we are here to make it happen.
The MTI Group’s Model 320BX Inertia friction welding machine used to produce oil pipes.
Advantages & Benefits
Powering Efficiency and Safety in Oil and Gas Operations
FWT’s friction welding technologies are revolutionizing the oil and gas industry with unparalleled precision and durability. Our innovative solutions offer a perfect blend of efficiency, quality, and sustainability, enabling companies to enhance their operations while meeting the industry’s demanding safety and environmental standards.
Reduced Preparation
The reduced preparation of friction welding is crucial for the oil and gas industry as it significantly cuts down on production time and costs. Friction welding requires minimal surface cleaning and alignment for parts, making it ideal for quick, efficient repairs and assembly of pipelines and drilling equipment. Components do not have to be thoroughly cleaned before friction welding as the process actually acts as a surface cleaner for joining components.
Forged Quality
Friction welding is highly beneficial to the oil and gas industry because it produces exceptionally strong, defect-free joints that can withstand extreme pressures and temperatures. This is critical for the integrity and safety of pipelines and equipment in harsh environments. The process also reduces the need for additional materials or filler metals, which can enhance corrosion resistance and durability. As a result, it minimizes maintenance costs and extends the lifespan of critical infrastructure.
Machine-Controlled Process
Friction welding provides the oil and gas industry with precise, consistent, and repeatable welds, crucial for maintaining the high safety and performance standards required. The process automation minimizes human error and ensures uniform quality across large-scale production, which is essential for critical infrastructure like pipelines. It also increases production efficiency and reduces labor costs by streamlining the welding process.
Green Technology
Friction welding is beneficial for the oil and gas industry as it aligns with the growing emphasis on sustainable practices and reducing environmental impact. Friction welding generates less waste and emissions compared to traditional welding methods, which helps in minimizing your carbon footprint. Additionally, its lower energy consumption contributes to overall cost savings and promotes more sustainable operation. Friction welding’s environmental advantages support regulatory compliance and improve the industry’s reputation regarding environmental responsibility.
The reduced preparation of friction welding is crucial for the oil and gas industry as it significantly cuts down on production time and costs. Friction welding requires minimal surface cleaning and alignment for parts, making it ideal for quick, efficient repairs and assembly of pipelines and drilling equipment. Components do not have to be thoroughly cleaned before friction welding as the process actually acts as a surface cleaner for joining components.
Friction welding is highly beneficial to the oil and gas industry because it produces exceptionally strong, defect-free joints that can withstand extreme pressures and temperatures. This is critical for the integrity and safety of pipelines and equipment in harsh environments. The process also reduces the need for additional materials or filler metals, which can enhance corrosion resistance and durability. As a result, it minimizes maintenance costs and extends the lifespan of critical infrastructure.
Friction welding provides the oil and gas industry with precise, consistent, and repeatable welds, crucial for maintaining the high safety and performance standards required. The process automation minimizes human error and ensures uniform quality across large-scale production, which is essential for critical infrastructure like pipelines. It also increases production efficiency and reduces labor costs by streamlining the welding process.
Friction welding is beneficial for the oil and gas industry as it aligns with the growing emphasis on sustainable practices and reducing environmental impact. Friction welding generates less waste and emissions compared to traditional welding methods, which helps in minimizing your carbon footprint. Additionally, its lower energy consumption contributes to overall cost savings and promotes more sustainable operation. Friction welding’s environmental advantages support regulatory compliance and improve the industry's reputation regarding environmental responsibility.
Our Commitment
Quality is at the core of our innovation
With an in-house innovation team and a substantial investment in R&D, we continuously set new industry standards in quality, systems, and best practices. Our commitment to excellence is reinforced by our ISO 9001:2015 certification. For customers in Europe, FWT machines are designed and manufactured to fully comply with European safety requirements for CE.
Friction Welding Machines for the Oil and Gas Industry
Machine-welded components are 100% solid-state bonded and are produced quickly and consistently, free of operator-made errors. This makes friction welding ideal for drill pipes, valves, and other drill stem components meant to withstand the high torque and rotary tension of directional drilling.
FWT offers the design and manufacture of friction welder machines, both semi and fully-automated, to meet the challenges of the oil and gas industry.
Friction Welding Machines for the Oil and Gas Industry
Machine-welded components are 100% solid-state bonded and are produced quickly and consistently, free of operator-made errors. This makes friction welding ideal for drill pipes, valves, and other drill stem components meant to withstand the high torque and rotary tension of directional drilling.
FWT offers the design and manufacture of friction welder machines, both semi and fully-automated, to meet the challenges of the oil and gas industry.
ROTARY FRICTION WELDING
FWT’s Rotary friction welding requires no prior joint preparation, saving time by not having to store pipes and other materials from the elements.
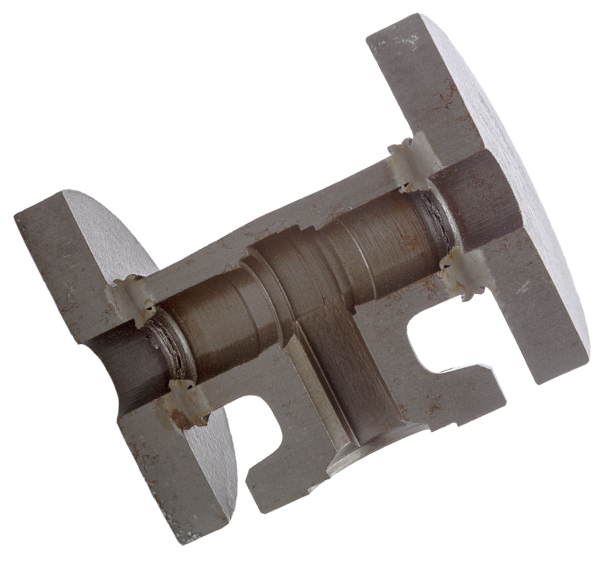
Explore Our Parts Gallery
View our parts gallery to uncover applications that might be right for your next project.
Contract Manufacturing Services
Our friction welding process equips you from start to finish. Whether you need to build friction welding machines or develop parts, we provide the in-house machines, lab, and knowledge necessary, including on-site service and training for operators and production assurance.
Contract Manufacturing Services
Our friction welding process equips you from start to finish. Whether you need to build friction welding machines or develop parts, we provide the in-house machines, lab, and knowledge necessary, including on-site service and training for operators and production assurance.
Oil and Gas Friction Welding Machines for R&D
Want to Make Oil and Gas Extraction Faster, Stronger, and Better?
Want to test your oil and gas project but don’t have the tools? MTI’s in-house friction welding machines are available for your R&D to optimize oil and gas extraction from rig site preparation to fracking. Test various materials and geometric fittings to ensure your project meets the demanding standards of your industry.
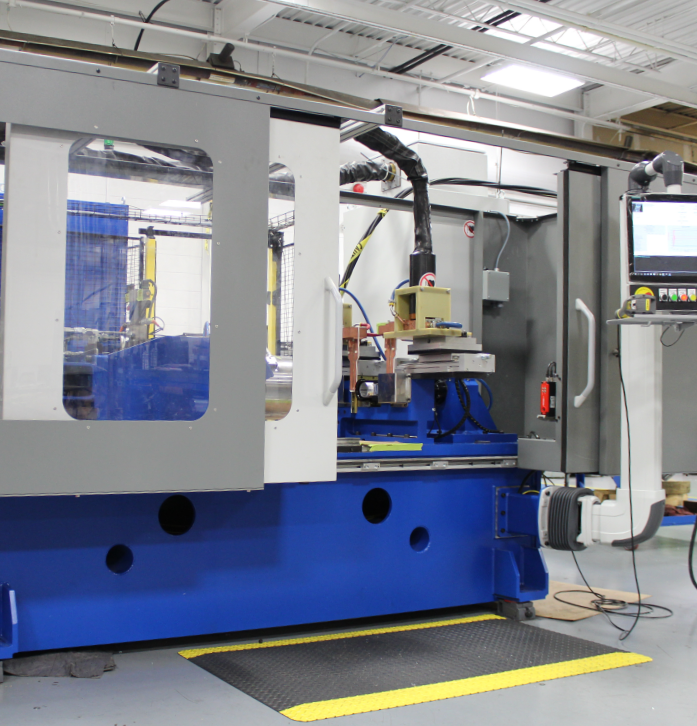
One of MTI’s Low Force Rotary lab machines.
Learning Center
Case Study
Videos
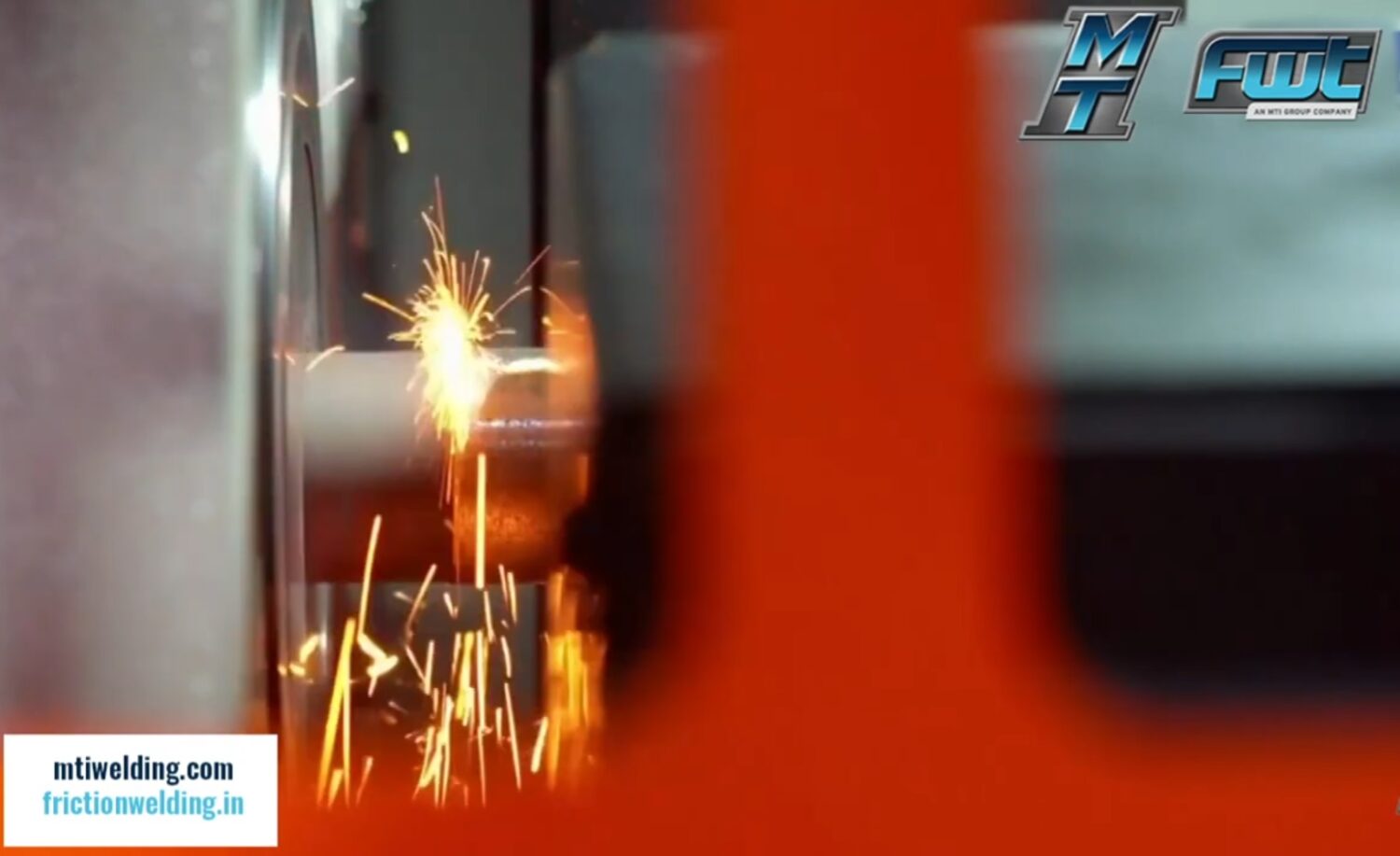
Direct Drive