MTINTERFACE™
An Industry 4.0 Solution
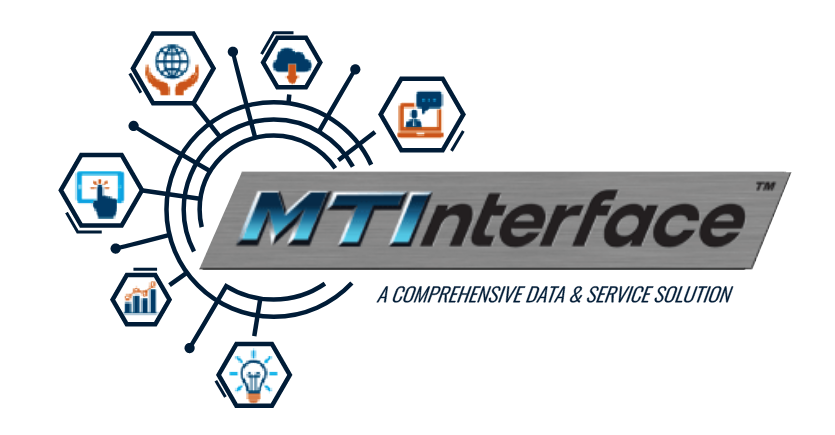
Industry 4.0
MTI now offers a comprehensive Industry 4.0 service solution for monitoring and improving machine performance!
Our new MTInterface™ Service Level Agreement (SLA) complements factory OEE requirements. It provides actionable, machine-level data and expert recommendations to ensure your friction welder consistently delivers your organization’s required performance and value.
Are you getting the most productivity and profitability from your MTI machine?
MTInterface
Machine Data Centralization and Real-Time Support
The Overall Equipment Effectiveness (OEE) score is crucial for manufacturers to track production performance. MTInterface leverages cutting-edge technology to uncover actionable insights into MTI-built friction welding machine performance by monitoring OEE signals: availability, productivity, and quality.
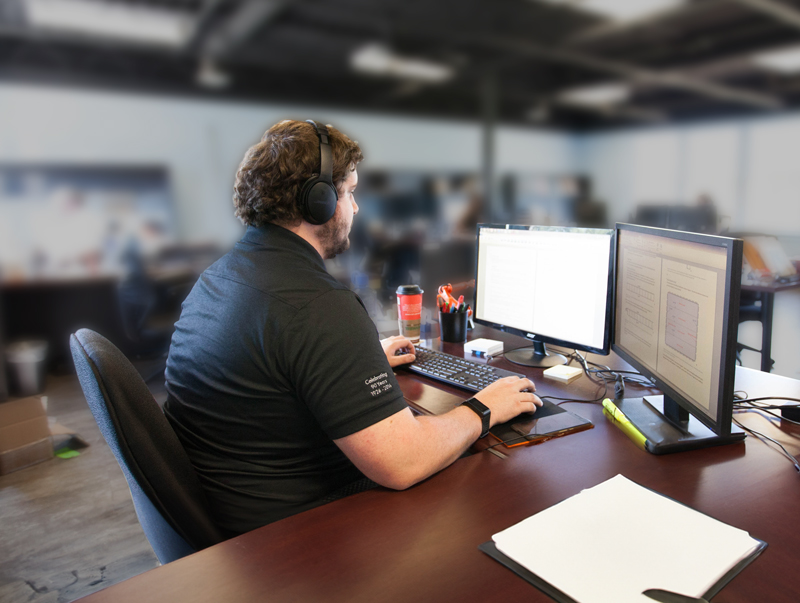
MTInterface Data Collection and Analysis
MTInterface complements Factory OEE requirements by centralizing machine-level data into a unified system. Data collection and analysis of your friction welding machine performance include:
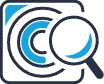
Machine Performance and Condition Monitoring
MTInterface continuously monitors both the performance and condition of your MTI machine, ensuring any potential issues are addressed before they impact weld quality or production.

Cloud Security
Utilizing the Industrial Internet of Things (IIoT), your MTI machine’s data is securely transmitted to our cloud server, allowing our support engineers to sync with your operations instantly.

Dashboard of Key Performance Metrics
Key performance indicators are presented in an at-a-glance dashboard, accessible from any authorized device, including computers, tablets, and mobile phones, providing real-time insights from any location.
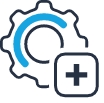
Add-On Options
MTInterface is customizable for add-on options that suit your production needs, from plant data integration to barcode serialization for part traceability.
MTInterface Data Collection and Analysis
MTInterface complements Factory OEE requirements by centralizing machine-level data into a unified system. Data collection and analysis of your friction welding machine performance include:
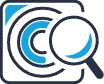
Machine Performance and
Condition Monitoring
MTInterface continuously monitors both the performance and condition of your MTI machine, ensuring any potential issues are addressed before they impact weld quality or production.

Cloud Security
Utilizing the Industrial Internet of Things (IIoT), your MTI machine’s data is securely transmitted to our cloud server, allowing our support engineers to sync with your operations instantly.

Dashboard of Key Performance Metrics
Key performance indicators are presented in an at-a-glance dashboard, accessible from any authorized device, including computers, tablets, and mobile phones, providing real-time insights from any location.
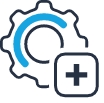
Add-On Options
MTInterface is customizable for add-on options that suit your production needs, from plant data integration to barcode serialization for part traceability.
MTInterface Service Support
Beyond data analysis, MTInterface enhances your operations with expert support from our engineers.
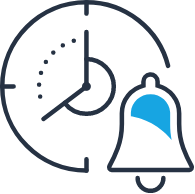
Real-Time Monitoring and Alerts
Our support engineers and technicians proactively identify and notify you of machine performance issues before they affect weld quality or production.
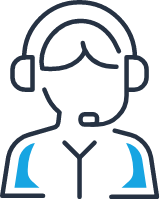
Priority Help Desk
MTI Help Desk responds within four hours, giving updates or resolutions within 24 hours.

Remote Support
Our support team provides expert recommendations and promptly addresses the issues with remote access through Vuforia Chalk.
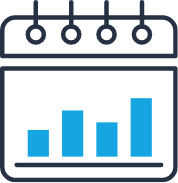
Monthly Service Action Reports
MTInterface delivers monthly action reports with insights on optimizing production, allowing you to track and compare the performance of your welding production assets effectively.
How MTInterface Works
MTInterface helps manufacturers and MTI support engineers quickly understand the welding machine’s performance.
It tracks and monitors data for you in real-time. MTInterface also transmits the data online to our secure cloud server, allowing MTI support engineers to access and analyze it.
Our service experts then provide their review of your MTI machine performance through monthly reports, including recommendations to increase uptime, enhance performance, and notify you of your next maintenance routine.
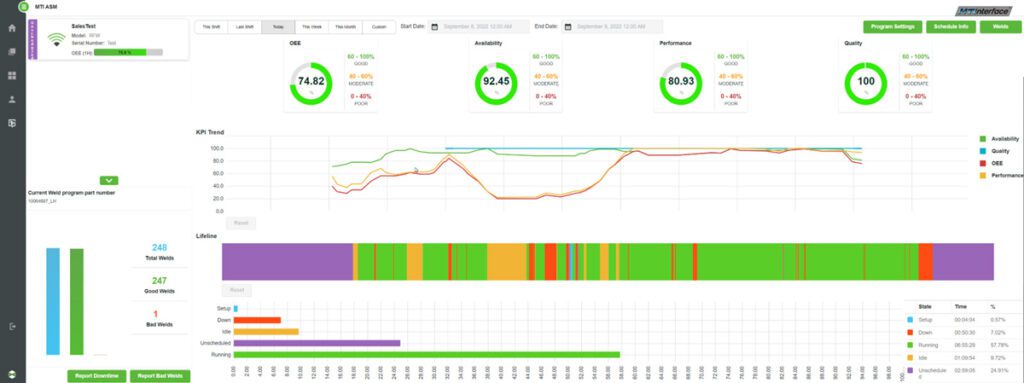
MTInterface SLA Subscriptions
We Offer Three Baseline Packages for our MTInterface SLA
- Full machine Performance and Condition Monitoring system connection
- 12 Monthly Service Reports
- 1 two-Day Onsite Visit (Travel expenses not included)
- 12 Hours Remote Service
- Help Desk Priority Support
- Discounted hourly Service rate at $180
- 5% Discount on Spare Parts
- Optional Customer OEE Integration at Additional Cost
- Full machine Performance and Condition Monitoring system connection
- 12 Monthly Service Reports
- 2 two-Day Onsite Visit (Travel expenses not included)
- 50 Hours Support (Remote or Onsite)
- Help Desk Priority Support
- Discounted hourly Service rate at $160
- 5% Discount on Spare Parts
- Optional Customer OEE Integration at Additional Cost
- Full machine Performance and Condition Monitoring system connection
- 12 Monthly Service Reports
- 3 two-Day Onsite Visit (Travel expenses not included)
- 100 Hours Support (Remote of Onsite)
- Help Desk Priority Support
- Discounted hourly Service rate at $150
- 10% Discount on Spare Parts
- Optional Customer OEE Integration at Additional Cost
Interested in an MTInterface SLA Subscription?
Learning Center
Featured Articles
Get the information you need, before you need it — free and straight to your inbox from industry experts.