From its humble beginnings in the mid-1900s to its new, cutting-edge capabilities that will one day help send the first human to Mars, Friction Welding has evolved plenty of times over the decades.
But as the technology shifts to meet the needs of modern-day manufacturing, the foundations of friction welding have remained largely the same. And although friction welding continues to produce excellent results, we continue to build upon it.
In this episode of Whiteboard Wednesday, we are focusing on the technology on which MTI has built its foundation: Rotary Friction Welding.
There are three main types of Rotary Friction Welding:
- Direct Drive Friction Welding
- Inertia Friction Welding
- Hybrid Friction Welding
Different parts and projects call for different forms of Rotary Friction Welding, and in this blog, we will highlight the advantages of each one to help you decide which one may be the best fit for your application.
DIRECT DRIVE FRICTION WELDING: HOW IT WORKS
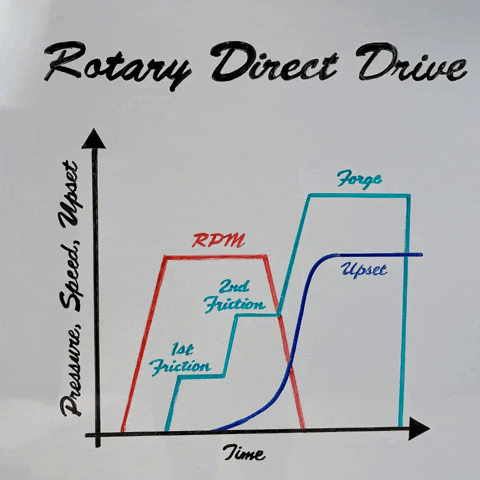
Each Rotary technology we will discuss in this episode has something in common – they are all based off Direct Drive friction welding. That’s because Direct Drive is the foundation of Rotary friction welding. It features:
- One component attached to a spindle
- An electric motor to drive it
- One component held stationary in the tailstock fixture
To begin the process, we rotate the part in the spindle up to a desired speed. With Direct Drive, we can go between two speeds – one associated with first friction and a different one for second friction.
First friction is at a low load and allows us to reduce the amount of torque at part contact when we are at a higher speed. It scrubs the components together to ensure the surface condition is conducive to reduce the coefficient of friction to start to build some heat.
Once that’s complete, we shift to a slightly higher load and switch to second friction, which is when we start to build up more heat in order to start upsetting material. We will stay in the second friction phase as long as necessary.
Direct Drive friction welding can be an attractive technology because we can customize the parameters to achieve our desired results.
For example, if we are welding a hardenable steel, we can apply some extra heat by using a longer second friction phase in order to help control the cooling rate.
In Direct Drive, we have a spindle limitation of the thrust bearing’s ability to react forge load when rotating, so typically we need to decrease our spindle speed to zero before we can bring on the forge load. At this point we increase to full forge load, squeeze out all of the softened material, and complete the weld.
Direct Drive friction welding, however, isn’t perfect for all applications… and that’s where our next technology comes in.
INERTIA FRICTION WELDING: BUILDING ON THE FOUNDATIONS
When Inertia friction welding was first invented, engineers studied some of the downsides to Direct Drive friction welding, primarily the torque peak at part contact.
To help overcome that issue, the inventors added a flywheel to the machine, which prevented high-torque applications from stalling the motors on friction welding machines.

As you can see in the graph above, in Inertia friction welding, all energy is stored in the rotating flywheel.
During the Inertia process, we disengage the drive and we bring on forge load, thus dissipating the kinetic energy stored in the flywheels as heat.
In order to shorten the weld time and get a narrower Heat Affected Zones (HAZ), we bring on forge load from the beginning instead of going through a step approach like we do in Direct Drive friction welding.
To accomplish this, we need a hydrostatic spindle because the thrust bearings can’t handle the high speeds and high load.
These innovations enable Inertia friction welding to scale the friction welding process to large-diameter components or large diameters with thin walls – mostly used in the aerospace industry. However, it can also scale down to use a thin wall tube welding into a plate, where a weld needs to be made very quickly.
Inertia friction welding utilizes some of the foundations of Direct Drive… so what happens when we combine some of the best parts of both Direct Drive and Inertia friction welding?
Meet Hybrid friction welding.
HYBRID FRICTION WELDING: WHAT SETS IT APART
With Hybrid friction welding, we have two key parameters of Direct Drive friction welding:
- The ability to manipulate the energy input through the load profile
- An electric motor driving at a constant RPM
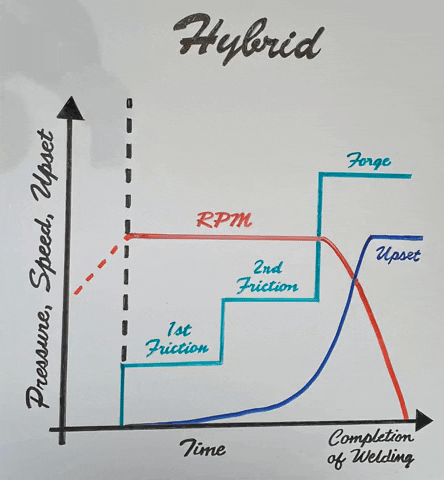
But with Hybrid friction welding, we also attach the flywheel so we can forge into the rotating spindle and get the extra hot working (modification of grain structure while the material is hot) like we see in the Inertia process, achieving a slightly stronger bond as a result.
Hybrid friction welding truly is a combination of Direct Drive and Inertia friction welding, allowing us to achieve a bit more hot working, if necessary, after putting in a variable amount of heat.
MTI CAN SUIT YOUR NEEDS
Now that we’ve explained the difference between Direct Drive, Inertia and Hybrid, you may now have a better idea of which technology would be the best fit for your application.
MTI can design, build, and deliver friction welding machines that utilize any of these three technologies (and beyond).
To start planning your machine, reach out to us today to be connected to a knowledgeable sales engineer to walk you through the process.
After you do that, be sure to check out the rest of our Whiteboard Wednesday videos and blogs to brush up on your friction welding knowledge!