There have been pivotal moments throughout history where new technologies were introduced, providing key advantages to those who had the vision to embrace it. Take the Automotive industry for example, as it shifted from steam power to fuel, and now emerging electrification trends. Those who have recognized the potential of new technologies early on have been able to capitalize on increased productivity, improved performance, and sustainability.
That’s the idea behind our new Weld Development 2.0 package. In this new package, MTI tests the feasibility of your application with traditional friction welding as usual, but we also perform Low Force friction welding test welds so you can compare the benefits of the new technology directly with the traditional friction welding processes.
Understanding the Traditional Weld Development
If you’re new to the idea of a Weld Development, or if you just need a quick refresher, we have a dedicated blog and episode of Whiteboard Wednesday to walk you through MTI’s process step-by-step. But here’s a quick recap:
The main purpose of a weld development is to optimize the results that ensure the production parts are fit for purpose by exceeding their in service performance. This includes testing your materials, geometries, part sizes, and more to validate that friction welding meets your requirements.
MTI’s Weld Development process happens in three phases:
-
- Phase 1 – Proof of Concept: In this first phase, our team leverages almost 100 years of engineering experience combined with state-of-the-art modeling and calculations to determine the optimal solution for your joining application. This phase will focus on the metallurgy and component geometry but can also consider the commercial and manufacturing impact of the process. This work effort may also include the welding of simple material specimens commonly referred to as coupon welds that are used to characterize the mechanical performance of the bond and confirm calculations.
- Phase 2 – Small-Scale Development: In Phase 2, we develop small-scale samples of your part to test their post weld performance and durability. These weld specimens may have the same geometry as the final part but are small-scale. This is particularly useful when developing bonds between exotic or expensive materials where we want to understand the behavior of the material during the weld process.
- Phase 3 – Full-Scale Development: In the last phase, we develop full-scale parts to test their viability on our range of laboratory and production friction welding machines. These components can be subject to real world service testing or prototype validation. It allows potential technical risks associated with your component’s design to be eliminated prior to manufacturing production-ready parts or an MTI machine purchase.
Traditionally, if friction welding is successful, we’ll start a conversation on whether you need a dedicated machine or contract services. When the appropriate friction welding process has been developed and successfully applied to your application, MTI can offer the design and manufacturing of a friction welding machine dedicated to your production needs. Alternatively, we can support your production using any of our 21 friction welding machines in-house.
But, here is where Low Force comes in…
Low Force Friction Welding
Though Low Force is our newest technology, it has already been adopted for multiple applications by those that have improved upon the process, observing the benefits and capitalizing on them to provide industrial advantage in their industry. In fact, there are thirteen Low Force friction welding machines that are operating in the industry today.
As we continue to optimize the Low Force process, we are seeing technical optimizations and advantages over traditional friction welding across multiple applications such as little to no flash formation, faster cycle times, superior mechanical performance, and overall part design improvements. But, the benefits don’t stop with your parts. Investing in Low Force has the potential to improve your entire manufacturing process.
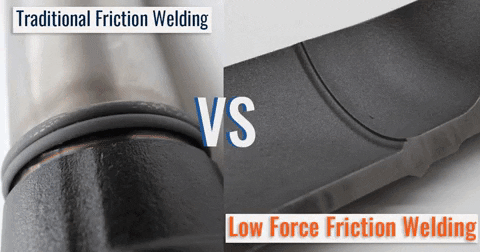
Axle comparison showing traditional friction welding on the left side and Low Force friction welding on the right.
With in-machine post-weld heat treatment, little to no flash, customization of post-weld characteristics and the ability to accommodate a larger part range, Low Force can eliminate entire steps from your manufacturing process. For example, in-machine heat treating may allow you to remove a secondary piece of heat treat equipment from your production line.
Quite often, the flash produced by traditional friction welding technologies needs to be removed from the components after welding. The Low Force process has a beneficial flash morphology that resembles a small, smooth bulge in comparison to the larger bifurcated flash curls that can eliminate the flash removal process completely for some applications. The Low Force welded component would be ready to move onto its next step while a traditional friction welded component would still be in-process.
Now, lets bring it all together.
Weld Development 2.0
We want you to get the most out of your friction welding process, which is where our new Weld Development 2.0 package comes in. It’s a process meant to uncover potential improvements not only in your current welding process, but your entire production line including part design enhancements and the elimination of pre or post-weld process steps. Now, you can test the feasibility of your application with traditional friction welding and Low Force side-by-side! You’re able to see the advantages of Low Force not just in the performance of your component, but also through your broader production line.
Our Weld Development 2.0 program will follow the same traditional phases, but with two technologies. Taking a closer look at Phases 1 and 2, you can expect side-by-side developments, tests, and results for both traditional and Low Force processes. Phases 1 and 2 will provide critical feasibility insight into your materials and part geometry with respect to the Low Force technology. MTI engineers will perform metallurgical tests including mechanical performance testing to ensure your part’s requirements are met.
As Phase 3 approaches, your team and MTI will work together to analyze the results of traditional and Low Force friction welding to decide the right path for your project. This will include a projection of the advantages that Low Force can offer in comparison to traditional friction welding.
Let’s Get Started
If you’re ready to discuss a weld development, or if you have more questions, we’re ready to help! Reach out to any of our knowledgeable sales engineers to get a conversation started today. Or, feel free to learn at home as we have multiple resources available for Low Force friction welding.
LinkedIn: https://www.linkedin.com/company/manufacturing-technology-inc
YouTube: https://www.youtube.com/c/ManufacturingTechnologyIncMTIJoiningSolutions/videos